Remanufactured parts market
The growing market for remanufactured spare parts provokes a different look at the automotive industry. Based on great imagination, let's assume two ecological scenarios for the development of the automotive market:
1) Producing cars from remanufactured parts (original parts return to the factory and can be reused in the production of another car)
2) Production car regeneration (the used car is completely regenerated at the factory and sold to another customer)
Referring to option 1, i.e. producing cars from regenerated parts, the availability of these parts is crucial. It will be necessary to build a relationship between the customer (dealer) and the car factory, and perhaps even create a parts sourcing network.
An in-depth ecological, economic and product analysis is needed to assess the validity of such a project. Taking into account the current knowledge about the remanufactured parts market, I assume that we can regenerate 60% of the parts (more in electric cars), and the regeneration cost will range from 50% to 90% of the price of the new product. I estimate that the parts return system to the factory will absorb 30% of the savings. It means that in economic terms we will significantly reduce production costs and the ecological benefits will exceed our expectations.
If we save 80% of raw materials in the parts used to produce a new car, we will reduce CO2 emissions by 50% compared to producing cars from new parts.
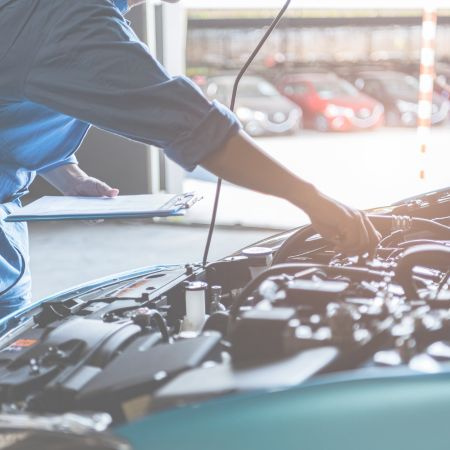
This is a very good result, which makes it worth considering about regeneration of car spare parts. Let’s take a look at the components of the parts regeneration process. What could a step-by-step production plan for remanufactured parts look like?
✅ Obtaining parts from the introduced new car sales system.
✅ Disassembly of the acquired part.
✅ Segregation of component parts according to the production plan.
✅ Regeneration of parts.
✅ Production of non-repairable parts of the assembly.
✅ Assembly of the component.
✅ Quality control.
✅ Sending to the first assembly warehouse.
For many, the question remains how many times can a part be regenerated? It is worth mentioning that the Automotive aftermarket will also need parts, but we will find the answer to this by producing a little more parts! 😊
Continuing the considerations regarding the production of cars from spare parts, an outstanding 😉 conclusion comes to mind in the form of an appeal:
Constructors! Fight with decision-makers and let your constructions be ecological in concept. Parts must be designed taking into account their future disassembly in the most automated way possible!
It is worth summarizing my considerations here with current data published at the end of 2021 by the European Parts Manufacturers Association CLEPA (SDCM is its Polish member). The published study shows that thanks to factory regeneration spare parts in 2020 over 800 thousand tons of CO2 emissions were avoided, which is equal to the carbon footprint left by 120,000 statistical inhabitants of the EU (source: https://clepa.eu/mediaroom/circular-economy-and-sustainability-are-reshaping-the-automotive-aftermarket/, 21/03/2024).
The mass use of remanufactured parts in the production of cars will save millions of tons of carbon dioxide emissions.
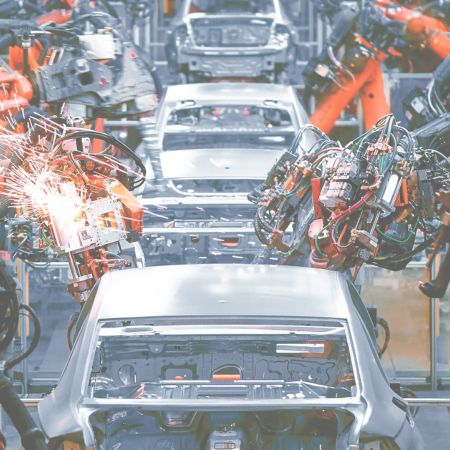
Share with us your opinion on this topic: are the ecological benefits enough to convince you to enter the market of remanufactured spare parts for cars? What is your opinion? Is the remanufactured parts market a sad necessity or an opportunity for ecological automotive development? What other questions are worth asking about the production of spare parts? Do you see any other problems with this?